What is neodymium's role in the energy transition?
Neodymium magnets are a vital component of electrification. Can the world meet growing demand for this rare metal sustainably?
Neodymium is not as widely known as other critical minerals such as lithium or platinum. Yet this rare material has a vital role to play in the energy transition. It is used to build powerful permanent magnets, found in wind turbines and electric vehicle batteries.
The proliferation of these clean technologies is integral to the energy transition and demand for neodymium is expected to grow 48% by 2050. But just like other so-called rare earth elements (REEs), mining it is a process with alarming secondary effects. At the same time, there are challenges around its supply, leading to risks of price volatility. As the race towards electrification intensifies, can the growing demand for neodymium be met sustainably and safely?
A lynchpin for clean energy
When combined with boron, neodymium creates a magnet powerful enough to hold more than 1,000 times its own weight. This property has made it an essential component in many modern electrical devices – from smartphones and computer hard drives to windscreen wiper blades – enabling them to be made far smaller.
In recent times, neodymium magnets have been scaled up for use in much more powerful devices, namely electric and hybrid vehicle motors and wind turbines. The material’s high magnetic strength relative to its mass makes it perfect for wind turbine generators for two main reasons. Firstly, it allows them to generate power more efficiently, producing a larger output of electricity while minimizing additional weight. Secondly, it enables wind turbines to be built with fewer raw materials, reducing their environmental impact.
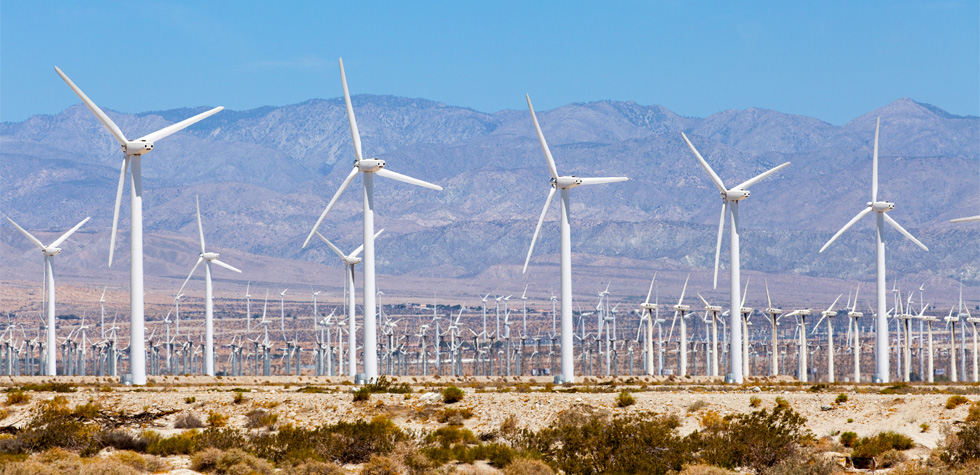
Not only are neodymium magnets powerful, they are also resistant to 'demagnetization', meaning they maintain their strong magnetic force for longer than other similar metals. This is critical for their applications in wind energy and electrified transport. It ensures turbines and EV motors have the longest possible lifespan, lowering maintenance costs which, in turn, helps them stay cost-competitive with fossil fuel counterparts.
A boom in demand
Governments across the world have set ambitious targets to expand domestic wind capacity and get more electric vehicles on the road. Policies like the United States’ landmark Inflation Reduction Act alongside similar measures in China and the EU are driving a surge in electric and hybrid-powered transport that could put as many as 700 million passenger EVs on the road by 2040. Meanwhile, wind and solar are on course to generate more than one-third of the world’s energy by 2030, nearly triple the amount they produce today.
But these ambitions hinge on a stable supply of REEs, neodymium chief among them. Currently, global REE production is concentrated in China (69%), the US (12%), Myanmar (11%) and Australia (5%). And global demand is growing far quicker than production. To put it into perspective, the IEA estimates that demand for neodymium could reach 850,000 tons by 2030, exceeding the projected supply by 250%.
Unless supply can catch up, spikes in the price of neodymium are likely, which would drive up costs for wind power and EV batteries. This could pose a major obstacle to the energy transition, which depends on these technologies being available at the lowest possible cost to compete.
Yet ramping up supply carries risks of its own. Stepping up production puts a strain on those industries and the mining regions. The way rare earths are mined – injecting chemicals into the earth to separate the materials from other elements – can be hazardous, both to local ecosystems and surrounding communities. In fact, the Harvard International Review estimates that one ton of REE produces 2,000 tons of toxic and even radioactive waste, which is at risk of contaminating soils and waterways.
Innovative solutions
In the face of these challenges, industry actors and policymakers are pioneering new solutions.
Although still in a relatively early phase, REE recycling is a critical strategy to make the neodymium supply chain more circular and sustainable. Programs like the EU-funded SUSMAGPRO project are robotically disassembling components and extracting neodymium magnets, in this case with a 25 percent higher recovery rate than traditional methods. Through initiatives like this (part of its Critical Raw Materials Act), the EU is aiming to meet 15% of its REE needs in 2030 with recycling. But, with just 1 percent of REEs recycled today globally, progress will be needed to make that possible, starting with designing new products with end-of-life in mind.
Others are developing magnets for wind turbines and EVs which offer similar properties to neodymium, but using more abundant, easily obtainable materials. A number of studies are identifying other potential candidates, such as tetrataenite and cerium, both of which can be mined more cheaply and sustainably than neodymium. Tesla, meanwhile, announced that it is designing its next-generation EV motors without any REEs at all. These technological innovations could help relieve pressure on the global neodymium supply chain.
Although the potential for recycling and substituting neodymium in vital clean technologies is great, emerging methods will need to mature rapidly over the next decade to meet burgeoning demand. International cooperation today is critical to make that possible. This can involve setting common standards to make supply chains more circular, international agreements to minimize disruptions and environmental risks and joint research projects to develop feasible alternative magnet materials.
Electrifying our power grids and transport systems is a critical pillar of the energy transition. But if action is not taken today to make the neodymium supply chain more sustainable, this little known, yet crucial, material could become a major obstacle.